Sturdy, low-cost vibration monitors for decanter centrifuges
With our simple, low-cost compact monitors, you can monitor imbalance of the centrifuge.
This is one of the most common causes of machine damage in decanter centrifuges as imbalance causes excessive vibrations when solids get stuck in the bowl or other machine parts during feeding, high-speed operation or discharge.
Local alarms and safety relays ensure that staff can operate the decanter centrifuge safely and prevent costly machine damage and downtime.
Contact
a consultant
PCH 1270/1272 vibration guard for Functional Safety
- Functional Safety level rating: PL-d / SIL 2
- UL/ETL listed
- Measuring parameter: velocity mm/s or acceleration m/s²
- Frequency range: 10 to 1000 Hz or 1 to 30/300 Hz
- 2 alarm levels with individual delay times and 2 alarm relays
- Analog DC output RMS 4-20 mA, proportional to 0-100 %
- Measuring range: 10/20/50/100 mm/s or m/s² rms
- Self-test function can be activated externally
- PCH 1272 only: RS485 communication for connection with PCH user software or cloud server
PCH 1275/1277 vibration guard EX for hazardous areas
- Functional Safety level rating: PL-d / SIL 2
- UL/ETL listed
- ATEX (zones 1 and 21) / IECEx / EAC CU 012 certified
- Measuring parameter: velocity mm/s or acceleration m/s²
- Frequency range: 10-1000 Hz or 1-30/300 Hz
- 2 alarm levels with individual delay times and 2 alarm relays
- Analogue DC output RMS 4-20 mA, proportional to 0-100 %
- Measuring range: 10 to 100 mm/s or m/s² rms
- Self-test function can be activated externally
- PCH 1277 only: RS485 communication for connection with PCH user software or cloud server
IoT-enabled decanter monitor for remote vibration analysis
Our advanced, 4-channel monitor, PCH 1420, provides you with a wide range of vibration data, detecting imbalance, bearing faults, gearbox faults, misalignment etc.
Trend data can be integrated into existing SCADA systems or be stored in the cloud, allowing you to analyse vibration patterns and diagnose machine faults remotely.
Our consultants
are here to help
PCH 1420 4-channel vibration monitor with IoT option
- Functional Safety level rating: PL-d / SIL 2
- UL/ETL listed
- 4 vibration input channels and 2 process input channels
- 4 configurable outputs, relay or 4-20 mA/0-2.4/5/10 V
- User defined bandpass filters from 0.7 Hz up to 11,500 Hz
- Bearing fault detectors: Envelope, Crest and Kurtosis
- Adjustable alarm levels and delay times
- Time waveform recordings from 4 channels simultaneously
- FFT analysis on local PC or in the cloud
- Connection to accessory boxes on bus system for additional process inputs, additional local relays, raw data on BNC connectors etc.
- USB/RS 485 serial connection
- ModBus TCP via the PCH EtherBridge for connection to cloud server (IoT)
Why monitor vibrations in decanter centrifuges?
Despite being critical assets in the wastewater treatment-, chemical-, oil-, and food processing industries, decanter centrifuges tend to be maintained at set intervals, so-called preventive maintenance.
But this may not be the best strategy. Here is why:
Unpredictable wear
Decanters are subject to centrifugal forces of up to 4000 x g and heavy loads, putting continuous stress on the machine components. Operating conditions are variable, which makes wear on the decanter components unpredictable.
Using preventive maintenance at set intervals means you must either replace decanter components more often than necessary to avoid breakdowns or run the risk of a component wearing out between maintenance intervals.
This can cause severe machine damage and endanger operators and other staff.
Protect your critical assets and staff with continuous vibration monitoring
By continuously monitoring your decanter centrifuge with simple, SIL 2-rated vibration monitors, you protect both machinery and staff with local Alert and Danger alarms. Safety relays ensure immediate shut-down of the decanter if vibrations exceed the adjustable alarm levels.
By choosing a more advanced monitor such as the PCH 1420, you can detect early signs of component wear before machine faults lead to unscheduled production stops or dangerous machine damage.
You can also repair or replace components based on their condition, so-called predictive maintenance.
Improve your OEM service offer
As an OEM or decanter service provider, remote access to vibration data in real time means you can offer a better service to your customers. You can analyse trend data of each machine and diagnose decanter problems remotely.
This means that your customer’s problem can be solved quicker, sometimes even without the need for on-site assistance.
Contact our
monitoring specialists
How to monitor vibrations in decanter centrifuges
Decanter centrifuges always have a natural level of vibration during operation. During start-up and shutdown, vibrations may amplify, but as long as vibrations stay within the OEM’s set limits, this is not cause for concern.
However, vibration patterns that amplify beyond the normal limits for the machine may be symptoms of imbalance, component wear or impending machine failure.
PCH vibration sensors are permanently mounted on the decanter centrifuge, collecting real-time vibration data, scalar values, and time-stream / waveform recordings. They can be factory fitted or retrofitted to any decanter regardless of its age.
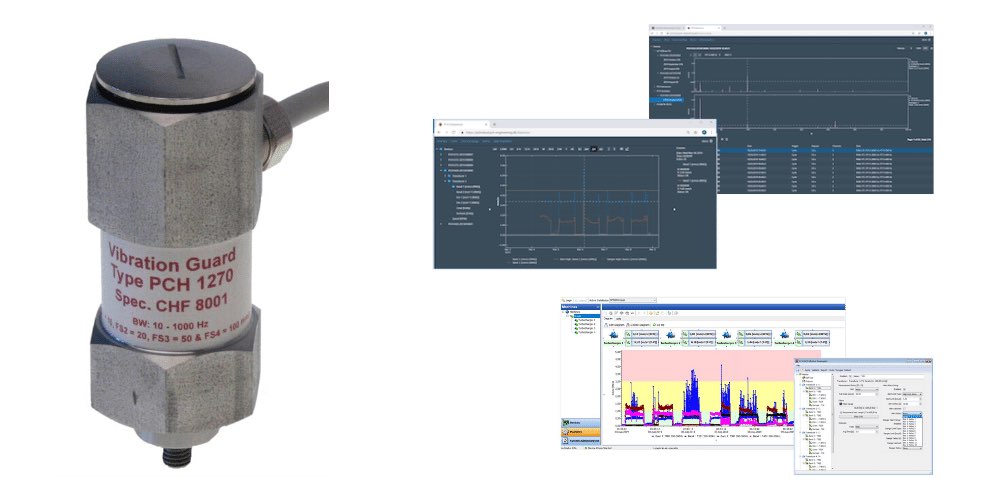
Monitor decanters for imbalance, bearing wear, gearbox faults and more
The simple monitors detect imbalance and protect your decanter through local alarms and SIL 2 safety relays. The more advanced monitors detect imbalance, early signs of bearing wear, gearbox faults, etc., giving you an accurate indication of where faults in the decanter centrifuge are to be found.
The vibration sensors integrate easily to existing SCADA or PLC solutions using standard communication protocols such as ModBus, TCP, RTU or OPC UA.
They supply trend data, which can be stored locally in a PCH Datalogger module or in the cloud for remote diagnostics.
Where to mount vibration sensors on decanter centrifuges
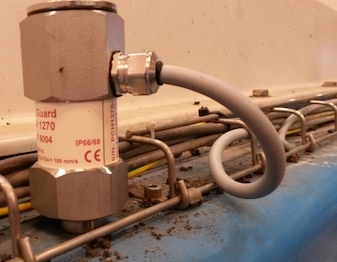
Where to mount vibration sensors depends on the type of decanter and on what you wish to measure.
To detect imbalance, sensors are typically mounted on the bearing housings at each end or on the foundation of the machinery.
To detect bearing or gearbox faults, sensors must be placed on the bearing housing.
Most common defects in decanter centrifuges
There are various reasons why decanter centrifuges fail. Gradually increasing vibrations may indicate wear and imbalance of the components, whereas suddenly occurring vibrations may indicate part breakage, chipping or bearing failure.
The most common decanter centrifuge faults are:
- Imbalance
- Bearing faults
- Gearbox faults
- Drive belt faults
- Mechanical looseness, misalignment
Imbalance in decanter centrifuge
Imbalance of a decanter centrifuge usually happens due to solid matter sticking to the bowl during feeding, high-speed rotation or discharge. Imbalance will amplify the vibrations, which not only hampers the performance of the machine but can also result in severe machine damage.
At lower speeds during feeding and discharge, vibrations are measured in the 1-100 Hz range. During high-speed rotation, vibrations are measured in the 10-10,000 Hz range.
Choose a monitoring solution that covers the range at which your decanter is most likely to unbalance.
Industrial decanter bearing faults
The bearings of a decanter centrifuge are subject to heavy, variable loads.
Vibrations from other parts of the centrifuge such as the conveyor shaft, bowl and gears will transmit to the bearings, which is why we mount vibration sensors close to the bearings.
The vibration analysis will help determine the exact cause of excessive vibrations.
Gearbox faults in decanter centrifuges
Gearbox failure can be caused by wear, faulty bearings, looseness, misalignment, lubrication issues, incorrect mounting of parts, failed seals etc.
Vibration analysis can detect early signs of gearbox failure and help diagnose the root cause of the problem.
Decanter drive belt faults
The belt drive system is crucial to the smooth operation of the decanter centrifuge.
If the belts are not tensioned properly, or if the pulleys are misaligned, it can cause stress on other decanter components such as the bearings and result in excessive vibrations.
Mechanical looseness or misalignment of decanter components
If any of the decanter components such as belt-guards, belts, motor mount plates etc. loosen during operation, or if the decanter is assembled incorrectly, it can cause misalignment and make the entire decanter centrifuge vibrate excessively.
Find a vibration monitoring solution to protect your decanter centrifuge from the most common problems
Contact
PCH Engineering