Recommended monitoring solutions for axial flow fans
As industrial axial fans are typically inaccessible during operation, we recommend you use permanently mounted vibration sensors and a vibration monitor that allows you to access vibration data remotely.
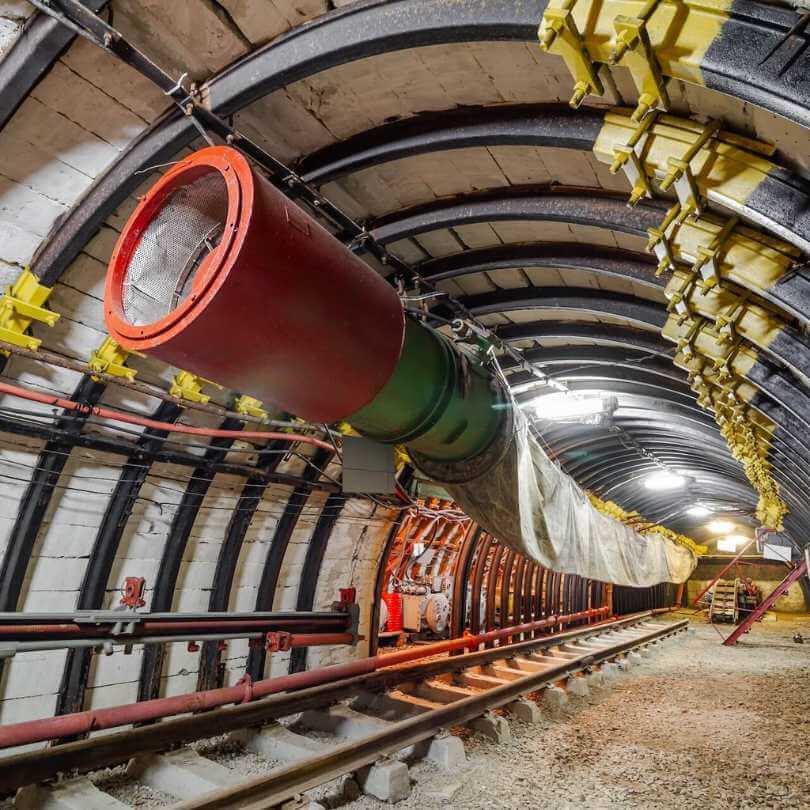
Common applications
- Underground tunnels
- Mining ventilation
- Wind tunnels
- Industrial ventilation
- Power plants
- … and more
Case: IoT monitoring of 18 critical axial ID fans
A wide array of IoT condition monitoring equipment was necessary to monitor 18 axial ID fans critical to the operation of a power plant in Saudi Arabia.
Continuous vibration monitoring: PCH 1420 Vibration Monitor
The
PCH 1420 Vibration Monitor isan advanced, 4-channel monitor which provides remote access to a wide range of real-time vibration data as well as local alarms.
With four channels for external, permanently mounted accelerometers, you can continuously monitor either four measuring points on one fan or one or two measuring points on multiple fans.
Features of the PCH 1420 Vibration Monitor
- Frequency range: adjustable, 0.7 Hz to 11.5 kHz
- Measuring range: adjustable (default 0-20 mm/s and 0-100 m/s²)
- Signal detection: RMS, Peak, Peak to Peak
- Measuring parameter: velocity (mm/s), displacement (μm/mm) or acceleration (m/s²)
- Other inputs: RPM via PNP/NPN sensor or 4-20 mA input
- Outputs: 4 analogue outputs (0/4-20 mA or 0/2-10 V) or 4 digital outputs, 1 alarm relay
- Communication: RS-485, USB, IoT-ready, PCH Cloud
- Compliance: SIL 2, IEC 61508, PL-d, IP 20
Advanced condition monitoring: PCH 1420 Vibration Monitor with buffered outputs and PCH Input Box
This solution is developed for large axial fans in process-critical applications. With the PCH 1420 Vibration Monitor with buffered outputs, you get remote access to all vibration data. At the same time your vibration analysts can access raw vibration data with handheld devices for advanced on-site measurements during operation.
The PCH 1420 with buffered outputs is suitable for Industry 4.0 environments and provides remote, online access to vibration data in real time when paired with the PCH EtherBridge IoT communication module.
The PCH Input Box provides further process input channels for measuring e.g., bearing temperatures with Pt100 sensors, flow or pressure from external transmitters.
Features of the PCH 1420 with buffered outputs
- Frequency range: adjustable, 0.7 Hz to 11.5 kHz
- Measuring range: adjustable (default 0-20 mm/s and 0-100 m/s²)
- Signal detection: RMS, Peak, Peak to Peak
- Measuring parameter: velocity (mm/s), displacement (μm/mm) or acceleration (m/s²)
- Outputs: 4 digital or analogue outputs (4-20 mA or 0-10 V DC), 4 buffered outputs, 1 main relay, additional input channels available via PCH Input Box
- Communication: RS-485, USB, IoT-ready, PCH Cloud via PCH EtherBridge
- Compliance: SIL 2, IEC 61508, PL-d, IP 20
Features of the PCH Input Box
- Input channels: 6 process inputs
- Input options: Pt100, 0/4-20 mA (with optional loop power output), or DC 0/2-10 V
- Operating temperatures: -10 °C to +60 °C
- Communication: I2C DIN rail bus
Online data access and IoT compatibility: PCH EtherBridge communication module
Combine the monitor with the PCH EtherBridge to upload and store your fan vibration data in the PCH Cloud database or on a local server of your choice, and easily incorporate vibration data into your predictive maintenance strategy.
Features of the PCH EtherBridge
- 1 alarm relay and 1 digital input relay
- Communication hardware: RS 485, RS 485/232, RJ45 LAN connector for TCP
- Communication protocols: Modbus TCP, Modbus RTU, OPC UA
- Data storage: PCH Cloud, IIoT Rest, mini SD-card (optional)
Let us help you decide on the solution best suited to your industrial fans:
Contact
a sales consultant
Why monitor vibrations in axial flow fans?
Industrial axial flow fans, also known as tubeaxial and vaneaxial fans or induced draft fans, ventilate tunnels, hospitals, cooling towers, thermal power plants and other large constructions.
They are typically installed in a duct, which means they cannot be accessed with handheld monitoring equipment. And without continuous monitoring in place, the first you will know of any problems is when the fan performance suffers.
In many applications, poor fan performance and fan downtime is a safety risk or a compliance and regulatory risk. Emerging faults increase the vibration amplitude of the fan, and continued operation could lead to fan failure and secondary damage to other fan components, increasing downtime and maintenance costs.
Continuous vibration monitoring provides early warning of emerging faults in axial flow fans, so you can cut downtime and maintenance costs to a minimum.
How to monitor vibrations in axial flow fans
As axial fans are inaccessible for manual service checks during operation, we recommend remote vibration monitoring with permanently mounted vibration sensors.
Vibrations should be measured with accelerometers mounted on the fan bearing housing of the shaft bearings and blade thrust bearings. As an extra safety measure, bearing temperature can be measured with Pt100 sensors.
Local alarms and shut-down features can help prevent catastrophic failure and improve local safety.
Common causes of vibration in radial fans
According to an American
study of industrial fan failure, the blades, shaft bearings, and blade thrust bearings account for over 52 % of axial fan problems.
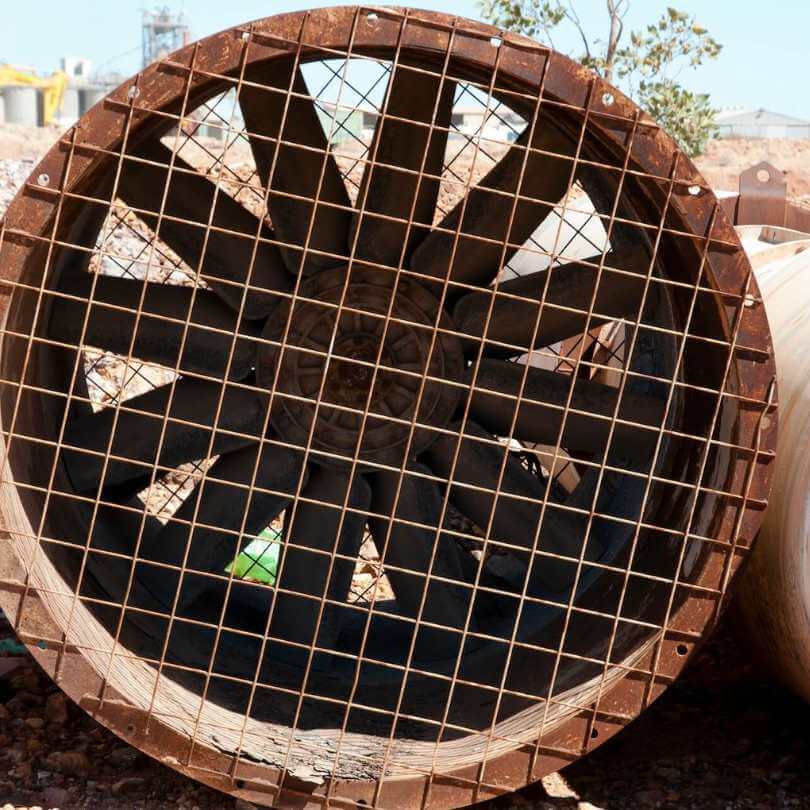
Bearing wear
The shaft bearings and blade thrust bearings of axial fans have a shorter lifespan than any other fan component. This is partly due to normal wear and tear, and partly to poor maintenance and improper lubrication. They also bear the brunt of any imbalance or other issues and should be replaced regularly.
Impeller imbalance
The impellers of axial fans can become unbalanced as a result of erosion, construction errors or poor installation. In power plant applications, even primary air fans that are supposed to handle only clean air, are prone to erosion as a result of fly-ash.
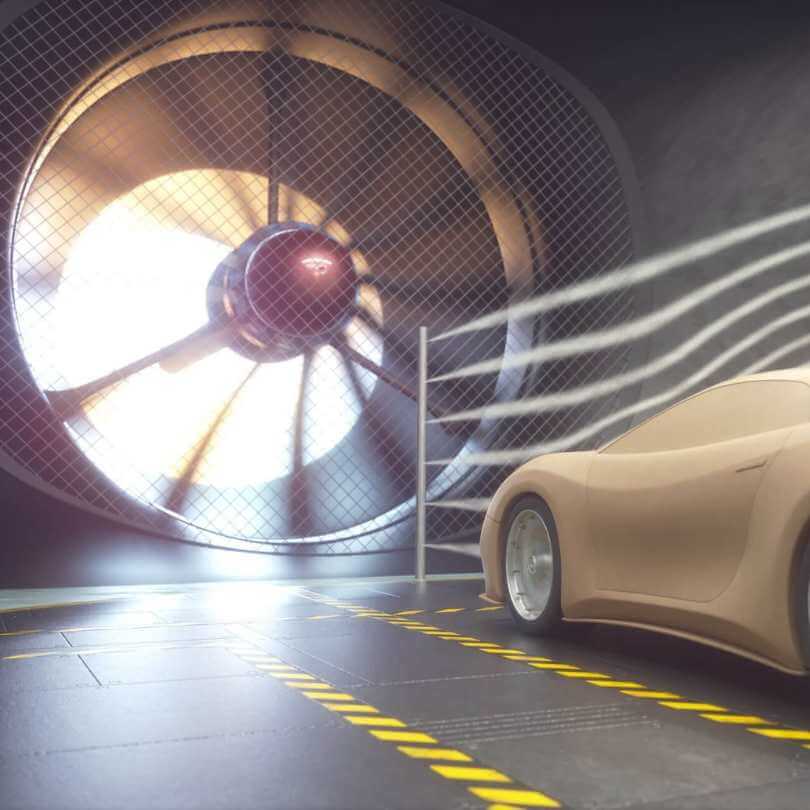
Resonance
Resonance is common in fans, as the lightly constructed fan components are naturally susceptible to this vibration issue, and it contributes to many fan problems.
It is often detected when the fan operates close to or moving through first critical speed during acceleration and deceleration. Resonance frequencies can also be caused by structural resonance, which can damage bearings, seals and other fan components.
Mechanically loose connections
Looseness in connections between bearing caps, bearing pedestals, foundation bolts, etc. can increase vibration amplitudes.